In this article Mohou.com will discuss with you the common materials, processes and post-processing for ceramic 3D printing.
In this article Mohou.com will discuss with you the common materials, processes and post-processing for ceramic 3D printing.
Materials
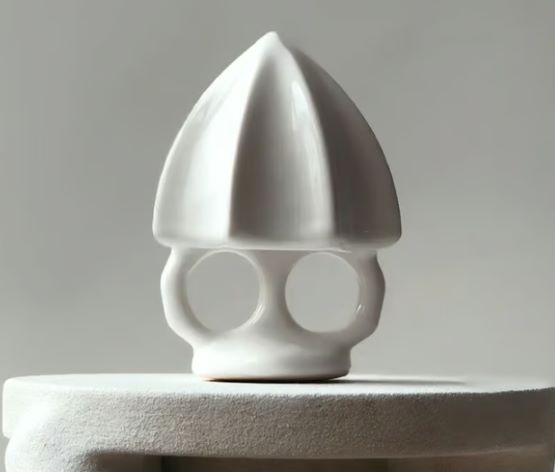
△ Ceramic materials used for 3D printing can come in many forms, including photoresins and powders
The unique aspect of ceramic 3D printing is, of course, the material. In the art world, the terms "ceramics" and "clay" are often used interchangeably to describe the different materials used to make pottery. Clay is indeed a type of ceramic, but not all ceramics are made of clay. In fact, ceramics contain a variety of materials that harden when heated at high temperatures, a process called firing.
The following materials are most commonly used in pottery 3D printing.
● Terracotta pottery is one of the most commonly used ceramics, usually for flower pots, it is porous and the material is readily available. It gets its red hue from the iron oxide formed when fired in a kiln. Terracotta can be extruded in an FDM system and is tougher than most clay ceramics.
● Porcelain is a mixture of silica and clay. It comes in three varieties: hard porcelain, soft porcelain, and bone china. Hard-glazed porcelain is the variety used for fine china and is made primarily of kaolin mixed with quartz and feldspar. Soft paste has a similar composition, but it is fired at a lower temperature, so the final product is not as hard as hard paste. Today, bone china is made from ashes, kaolin and feldspar. Porcelain can be manufactured using an FDM extrusion process, or 3D printed in the form of ceramic light resin, or bonded together in powder form with a spray of adhesive.
● Pottery is typically refined with clay (a highly fluid mixture of clay and water) prior to firing to improve surface texture and make it water resistant. It is fired but not vitrified (turned into glass) during this process, so it has a rougher surface than porcelain. It is possible to 3D print extruded manufactured pottery, and WASP is one of the most famous companies producing ceramic 3D printers.
● Stoneware is a non-porous pottery that is fired at high temperatures. Although it is waterproof, glazes are often used for aesthetic purposes. Stoneware is most commonly used in 3D printing.
Ceramic filaments
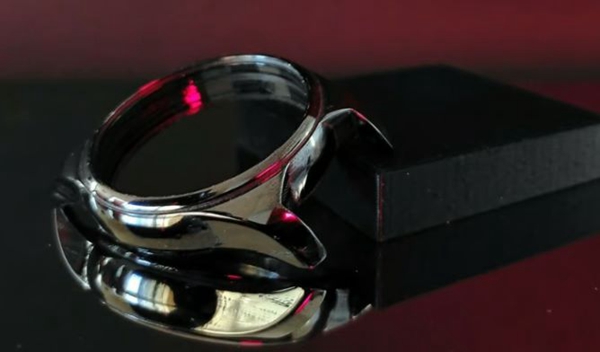
△ Besides pottery, ceramic filaments are also well suited for other aesthetic applications, such as this case
In addition to ceramic materials that can be extruded directly from a special 3D printer, there are also ceramic-based filaments that can be printed on a regular FDM 3D printer. These filaments are typically composites of polymer-based adhesives and ceramic materials. Like other filaments, they are wound on a spool of wire, but usually become very brittle before they go through the final heating stage. During firing, the polymer is burned off, leaving only the ceramic material, and some filaments require a separate degreasing process to separate the polymer from the ceramic material.
There are several companies on the market that produce ceramic filaments, including Spectrum Filaments, LayCeramic and Zetamix. these filaments tend to be much more expensive than standard pottery materials such as earthenware. LayCeramic with a diameter of 2.85 mm costs about $140 per kilogram, while Zetamix zirconia-based filaments with a diameter of 1.75 mm cost about $650 per kilogram.
Ceramic 3D Printing
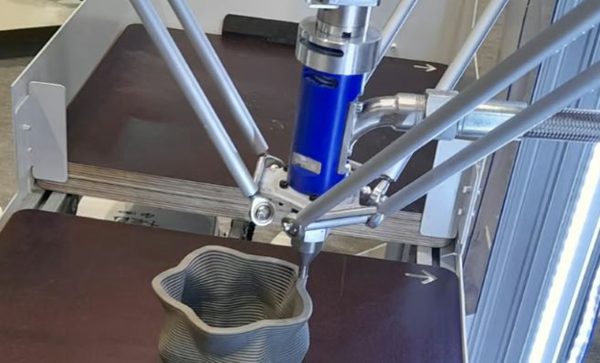
△Wasp clay extruder
Today, ceramics are 3D printed in a variety of ways, each with its own advantages and disadvantages. The most cost-effective way to print ceramics is through extrusion, but it also has the lowest accuracy. Resin printing and adhesive jetting can provide a higher level of accuracy, but are expensive.
Extrusion 3D Printing
Clay extrusion-based 3D printing systems are the most common way to make ceramic parts for pottery applications. One of the most popular clay extrusion systems is Wasp's delta line of clay printers, which can use pneumatics to push the clay out of the extrusion nozzle, or a motor-driven spiral structure to push out the material.
The advent of ceramic filaments has made it possible to use ordinary FDM machines to print pottery as well. However, due to the degreasing process, the prints shrink and become smaller. For example, when all the polymer is burned off, LayCeramic filaments shrink by up to a quarter, so more care must be taken when designing the geometry of the pottery so that it stays in one piece during the shrinkage phase. wall thicknesses need to be thicker by design, and Zetamix recommends that its zirconia filaments be designed with a thickness of 2 mm. wider nozzle diameters are often preferred when using these composites, with a recommended 0.6mm nozzle instead of the standard 0.4mm nozzle, and the nozzle should be hardened steel or a steel that can withstand abrasive materials.
Other 3D printing
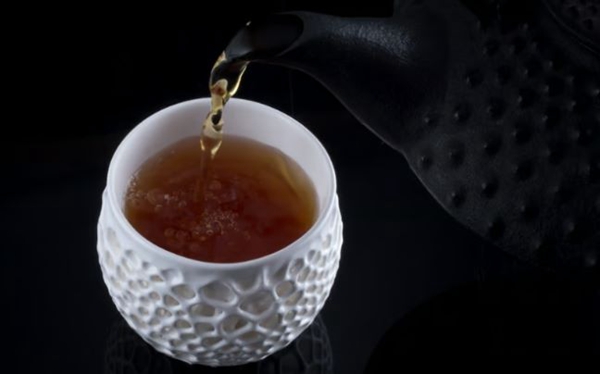
△ Higher precision printers mean higher prices
Ceramics can also be produced using compatible resin 3D printers and adhesive injection systems. These machines tend to be used more for technical ceramic applications, but small, highly detailed decorative ceramic components can also be produced using photopolymer systems. Ceramic and polymer blends, such as Formlabs' ceramic resin and Tethon3D's Porcelite, need to be prepared prior to printing. ceramic resin can make the printing process difficult due to its heaviness, which is much heavier than most plastics, making it challenging to get the part to coat smoothly and flatly on the workbench.
Binder injection systems can also be used to print ceramic parts, such as Kwambio's ceramic printers, which utilize a powder bed system to produce high-precision ceramic parts. The powdered ceramics are bonded together layer by layer with proprietary adhesives to maintain the shape of the printed part, the "raw state," until it is ready for glazing and firing. Binder jet ceramics is a very specialized process that requires specialized machines, so not every binder jet printer can produce them. While it is possible to make pottery using these 3D printing methods, the machines required are very expensive - typically starting at five figures. As a result, these methods are out of reach for the average consumer.
Post-processing
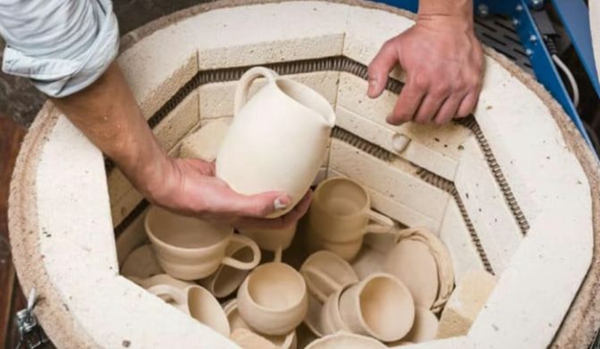
△ As with traditional pottery, 3D printed pottery must be fired in a kiln
For extrusion systems that directly print ceramic materials, the prints can be dried for one to two weeks, depending on the material used and the size of the part. The dried prints are then fired in a kiln, a process called vegetal firing. Finally, the glaze is applied and the prints are then glazed and fired. Kilns are expensive, so many people choose to outsource the firing process. Since the process is often the same as firing any traditional ceramic, specialized kilns and glazes are usually not required.
Post-processing is slightly more complicated for ceramic filaments printed using a regular FDM printer. Certain filaments require degreasing prior to firing the prints. For example, Zetamix's zirconia filaments require a two-stage process after the part is printed. First, the part must be placed in an acetone chemical bath to dissolve the adhesive, and then fired in a crucible filled with powder to thermally remove the remaining adhesive, with the entire post-processing taking more than two days. Be sure to read the manufacturer's instructions carefully before starting to use ceramic composite filaments, as the application of specific materials can vary greatly.
Applications
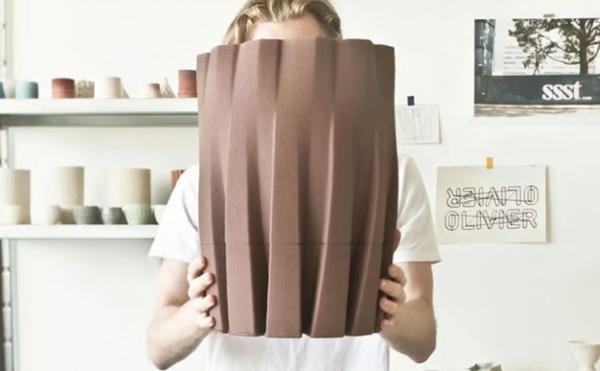
△ 3D printers have become part of the artistic practice of some potters
Ceramic 3D printing has inspired a new generation of artists, sculptors and architects to create ornate and detailed objects in shapes that would be impossible to achieve using traditional ceramic processes. From pottery to architectural applications, designers are finding new ways to make ceramics, and ceramic artists such as Jonathon Keep, Kate Blacklock and Emre Can have been using the 3D printing process to create ceramic pieces for museums and private collections with stunning and unique results.
In recent years, 3D printers have been used to extrude clay to create unique roof tiles, artificial reefs, and even entire buildings, such as the blue ceramic arches in the historic Dutch city of Delft and Ceramic Morphologies' 3D printed ceramic pavilion, which demonstrate the potential of ceramic 3D printing.
Printing Services
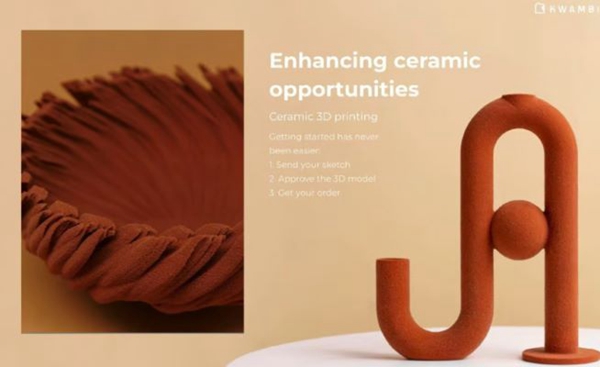
△ A Simple Approach to Ceramic 3D Printing
Since 3D printing and post-processing ceramics is a rather complex process that requires specialized machines and knowledge of how the prints react in the kiln, 3D printing services have emerged in the market. If you're just trying out an idea and don't want to buy the full setup yourself, then this is definitely the way to go.
Kwambio is a specialized ceramic 3D printing service company that has developed their own ceramic 3D printer based on powder bed technology, they have a ceramic part design guide on their website, and if there are any issues with the design, their engineers will provide you with feedback before producing the part. All you need to do is upload a file or sketch on their website and wait to receive your ceramic part.
Printer Options
As mentioned above, the 3D printer can print anything from kaolin and porcelain clay to stoneware and terra cotta.